Lab Energy Optimization & Efficiency: How to Do it Safely
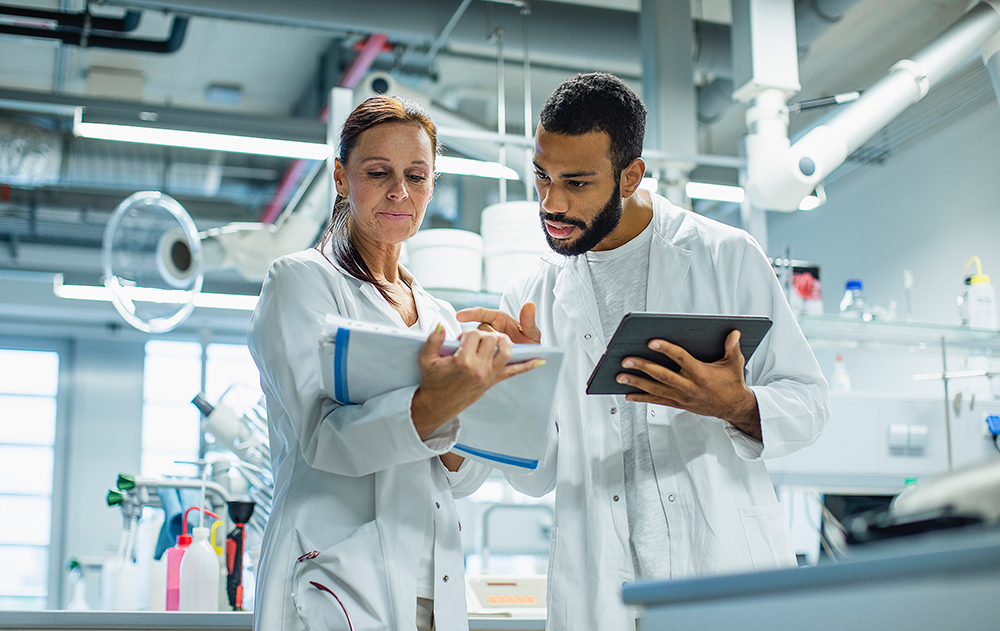
College campuses across the country are instituting green initiatives and signing aggressive carbon reduction goals to become better stewards of the environment. However, there’s evidence that these initiatives can be easily derailed by some of the largest energy users on campuses: laboratories. That’s because the primary method for reducing energy usage in labs involves modifying the ventilation – a change that can raise safety concerns. These concerns typically, and understandably, can lead to a standstill. Institutions don’t want to make changes that potentially put researchers and students at risk, so they decide to do nothing and live with inefficient energy consumption.
Yet, this course of action assumes there are only two choices — make your laboratories less safe or ignore potential energy savings. Luckily, there’s a third option: bring in professionals to conduct a laboratory energy optimization risk assessment. With professional insights from a team comprised of environmental health and safety consultants and mechanical engineers, colleges and universities can receive clear, accurate answers on energy savings opportunities that won’t negatively affect safety conditions – and can in some cases make them safer.
The key to this process is recognizing that laboratories are varied, unique spaces that can’t be lumped into one category. They serve different purposes, they work with different materials and, because of this, some are better candidates for energy optimization than others. One blanket solution isn’t going to apply to all of the labs on your university’s campus. When each lab is analyzed individually, a plan can be developed that takes each unique space into account without compromising safety.
To give you an idea of how this process can work for your institution, we’ll walk you through the basic steps an environmental health and safety and engineering firm would use to assess your campus’ potential for energy optimization.
A Peek Into the Process: Safely Determining Lab Energy Optimization
The first and most important step toward campus lab energy optimization is to obtain buy-in from all stakeholders in this process. The potential to make changes often raises concerns from laboratory stakeholders, so addressing these concerns is essential for moving forward. Stakeholders might include upper management, researchers, environmental health and safety, and facilities management.
The next step should be ensuring the right environmental health and safety experts are in place to support your project. Since many of the recommendations made for reducing energy consumption will likely involve modifications to the building’s mechanical systems, finding a firm that also offers engineering services can save you a step. For instance, here at EH&E, our health and safety experts work alongside our engineers to provide the best solution in the most efficient manner.
Our laboratory energy optimization process involves two steps: control banding and engineering analysis. The control banding process is a review of the chemicals, materials, equipment, and procedures used in a laboratory that aligns laboratory hazards with appropriate ventilation controls. This review includes interviews with key people to understand the purpose and standard operating procedures of each laboratory on campus. Specific research processes and materials are examined to assess the needs of the researchers and the chemical inventory. We also look at specific engineering controls and where they are located within each lab.
Once the analysis is complete, laboratories are assigned one of four different control bands, with level 1 presenting the least risk and 4 presenting the greatest risk. Lower ranked labs are considered stronger candidates for energy optimization, while higher ranked labs may require a cost benefit analysis to determine if the more complex changes necessary to maintain safety will be worth the investment. Labs in the highest risk group are often considered poor candidates for energy optimization.
Next, each lab undergoes an engineering assessment to document current ventilation rates, cooling and room pressure criteria and the current sequence of operation. Engineers look at the heating, ventilating and air conditioning (HVAC) system and building infrastructure to determine what adjustments can be made and at what cost.
Finally, we deliver a Laboratory Ventilation Management Plan (LVMP) to ensure continued performance and energy savings in each lab building. The LVMP details the performance of the lab mechanical ventilation systems over time, which can help identify changes in system performance that may indicate a problem that needs to be resolved.
While laboratory buildings are undergoing the energy optimization process it is a great time for labs to consider incorporating ASHRAE 241-2023 recommendations. Optimizing ventilation and filtration levels in the case of high-risk infectious aerosol conditions, for the offices, lecture halls and meeting rooms in spaces adjacent to labs is an efficient use of resources and will harmonize project objectives. Essentially you will be able to get both projects done at the same time at a fraction of the cost of handling each project alone.
Through this process, we generally discover that around 60 percent of labs on campuses are good candidates for energy savings. A common finding is that despite their different purposes, laboratories are often designed and built with identical ventilation and airflow standards. In comparison, a control banding risk assessment evaluates individual labs and the specific work activities to align different ventilation rates.
Putting It in Practice: Balancing Energy Optimization with Safety
Universities that apply the approach described above find that they can significantly reduce energy usage and, in some cases, enhance lab safety. For example, EH&E helped a large research university in the Northeast evaluate opportunities to reduce energy usage in approximately 40 lab spaces. Control banding revealed that a night set back ventilation rate for lower risk laboratories and certain support spaces could reduce HVAC energy usage.
In addition to this set back, EH&E’s team adjusted fume hood exhaust performance. The team also performed several maintenance activities, such as cleaning clogged fan coil unit filters and replacing failed control valves.
These changes led to an approximately 40% reduction in the buildings’ annual energy usage intensity and an annual energy savings of about $262,775. These changes are expected to reduce associated emissions by 4,972,100 kg CO2e (kilograms carbon dioxide equivalent) for a 5-year period which is equivalent to taking approximately 225 cars off the road.
In addition to the cost savings, simple adjustments to how high-risk chemicals are stored have made the facility safer. The project has also increased awareness among building occupants and staff about the importance of preventative maintenance in maintaining a healthy indoor environment.
Move Forward Safely
Aligning safety, engineering, and stakeholder interests will help your laboratory green initiative plans get off the ground smoothly. Be sure to choose an approach that considers individual researcher variables to fully prioritize both safety and energy optimization. With the help of professional environmental health and safety and engineering experts, your institution can experience a trifecta of benefits: becoming better stewards of the environment, keeping students and researchers safe, and saving on energy costs.
Want to learn more about how EH&E can help you achieve your carbon reduction goals? Contact us today!
Subscribe
to our blog
"*" indicates required fields