Successful Laboratory Energy Reduction Programs Start with Buy-In
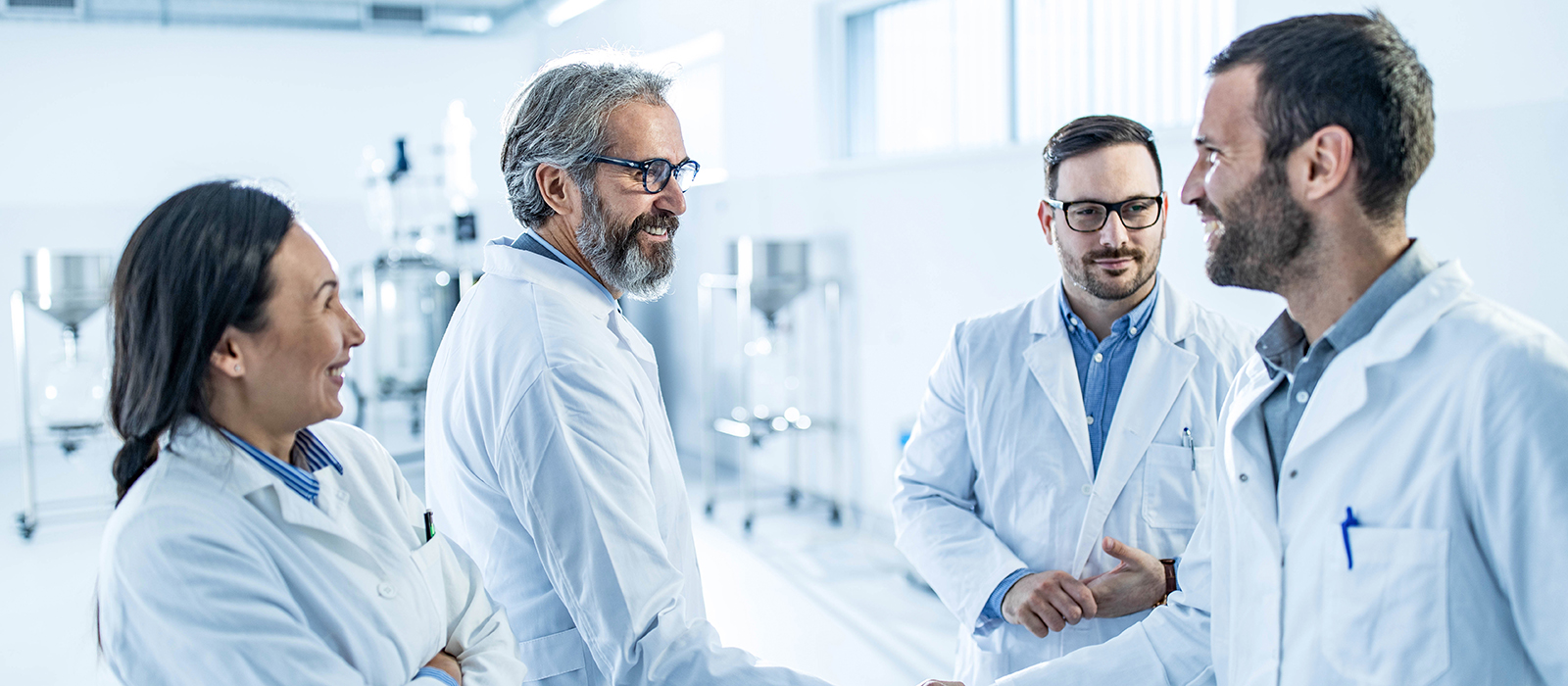
Laboratories are high-intensity energy users, which makes them one of the best places to make significant inroads in carbon-reduction initiatives and energy-cost savings. But executing a successful energy-savings program for laboratories is challenging, largely due to the complexity of the environments and the sensitive operations performed combined with the need to prioritize and ensure safety.
Among the numerous hurdles includes correctly qualifying laboratory spaces for energy conservation measures (ECM) such as occupied ventilation setback, unoccupied ventilation setback, and total exhaust reduction to fume hoods. Determining if a lab space is a good energy-conservation candidate based on energy usage can be tricky as it may have issues that may disqualify it.
Another obstacle that frequently is underestimated is the need to secure buy-in from all the numerous stakeholders right from the start. Without buy-in, stakeholders can delay the project or unintentionally undo any achieved energy savings. An energy savings program should start with careful communication with stakeholders to identify and address their needs because each of these stakeholders have different concerns that must be addressed upfront.
It also should employ a control banding process to properly categorize and qualify laboratories for energy- savings opportunities while ensuring safety. While this control banding process is a systematic and efficient way to assign risk, the potential to make changes often raises concerns from laboratory stakeholders. It’s critical that the control banding process begin by ensuring alignment from all parties that could potentially be impacted by changes to the lab environment.
The Key Stakeholders
There are four main stakeholders to include and they each will have their own set of needs to consider. These four groups are:
- Laboratory occupants
- Environmental health and safety (EHS)
- Facilities and Maintenance (FM)
- Upper management
Most programs make the mistake of overlooking facilities and maintenance staff and laboratory occupants, yet these groups are essential to supporting ongoing energy savings. The laboratory occupants are the end users, making them a vital stakeholder in the process. Being safe and feeling safe while working in their environment is paramount. Without their buy-in, the project can be delayed or derailed by the laboratory occupants objecting to the project on the bases of their safety being compromised. Also, if they feel unsafe in their workspace or feel their voices are not heard, control measures such as occupancy or sash position sensors may be tampered with to override or disable any ventilation setbacks. If this occurs, unsafe working conditions may be unintentionally created and expected energy savings may be negated.
Communication is essential to obtain buy-in from lab occupants. All stakeholders must be aware of why the project is occurring, how it will affect them, and how safety will be maintained throughout the project and once it is complete. Feedback must be encouraged and addressed. Safety must be prioritized, and the control banding process is a tool to help ensure any optimization of laboratory ventilation is done safely.
The next stakeholder to consider is the institution’s EHS group. If there is any potential to increase risk—and any system change carries the potential to increase risk—these professionals may be reluctant to push for a change. The primary concern for EHS is to maintain and verify safe work environments both during the project and after the project is complete. To obtain buy-in, their concerns can be addressed by a thorough review and execution of the control banding process, the creation of standard operating procedures (SOP) for how work is to be performed within the laboratory spaces, and the development of policies and training methods for how safety is maintained and verified.
Methods to verify safe working environments may include ongoing trending of mechanical equipment performance, visible and audible alarms, regular fume hood face velocity testing, and ASHRAE 110 fume hood testing. Without buy-in from EHS, lab ventilation recommendations can be rejected due to misconceptions, causing the project to be delayed or disrupted.
Another important stakeholder is an institution’s facilities and maintenance (FM) group. Facilities managers are likely to be the greatest ally in the goal of reducing energy usage, because this group prioritizes low operating costs. Facility managers likely will be expected to maintain any new building systems to be implemented as part of the project so it is important to communicate how the project will impact the building and how any new systems must be maintained. This may include the need for increases to maintenance budgets or the need for maintenance service contracts. Without proper maintenance such as regular inspection and calibration of sensors, mechanical systems can improperly control airflows within labs and the information they provide that is used to verify safe working conditions can be inaccurate.
The final stakeholder group is upper management. Administration tends to drive energy reduction efforts, because much of this work begins in support of broader organizational sustainability goals. With their support, and a clear understanding of how this work fits into big-picture objectives, and still maintains the appropriate level of safety, most other stakeholders tend to fall in alignment. Consistent communication between stakeholders is key to the success of laboratory energy-reduction programs. If all stakeholder needs are not met, valid ECMs can be blocked or undone leading to the program yielding disappointing results by not achieving the expected savings, or worse, unintentionally causing safety concerns.
Normally a representative from each main stakeholder group is part of the Project Team, which also includes representatives from internal and external resources such as consultants and contractors all working towards successfully executing the project. Active participation from the four main stakeholder groups in the project team should be highly encouraged and any consultants and contractors should be experienced in complex laboratory environments.
How the Control Banding Process Works
The control banding process is an assessment method used to manage workplace risks using data inputs relating to operations, hazards, and controls in the laboratory reported by their occupants as well as chemical inventory information. Control banding is a critical component to energy reduction programs in laboratories because it determines the health and safety risks used to develop recommendations for general ventilation and engineering controls. The first step in assigning a space to a control band category is to determine whether a space is eligible for ventilation optimization or setback by meeting fundamental laboratory health and safety requirements.
Here are the three essential steps of the control banding process.
Step 1: Evaluate Laboratory Operations
The goal of this crucial first step is to get a clear picture of each laboratory’s purpose and procedures. This involves interviews with key occupants to understand the needs of the researchers. These interviews provide the opportunity for direct communication to help establish program goals and secure buy-in. Laboratory walkthroughs are performed to review specific research processes, materials, and chemical inventories. Also examined is how specific equipment is being used and where it is located.
Step 2: Risk Analysis
The second step is to review the data collected from step one and conduct a risk analysis to determine appropriate controls to contain contaminants at the source. A risk-assessment matrix is used to conceptualize how to determine risk in a laboratory based on the severity of hazards and likelihood of hazards of causing an injury or adverse outcome. Based upon this information the level of risk in a space can be classified. Different hazard categories are ranked and play a role in the level of hazard severity. Chemical hazards are commonly present in these spaces and can be categorized by their health risk and exposure potential. Developing a chemical profile for a laboratory space helps to identify good candidates for energy reduction.
The risk assessment matrix also looks at factors that influence the likelihood of an injury or adverse outcome to occur. An example of this is the intensity of use of a chemical. How much of a chemical is being used and how often it is being used? Increasing severity of hazards and increasing likelihood of an injury or adverse outcome increases the overall risk of a space.
Laboratories are then put into a control band or risk group ranked one through four. The lower ranked laboratories are considered good candidates for energy reduction whereas the higher ranked laboratories may be considered too risky for energy reduction. The risk assessment process helps identify weak and strong candidates for energy reduction based on the work occurring in the laboratory.
Step 3: Determine Viability of Energy Opportunities
Typically, conceptual hazard levels one through three are considered good candidates for energy reduction but some spaces that are deemed ineligible may be able to make modifications that would make them eligible. For example, by implementing controls (such as engineering controls and administrative controls) to improve safety, a laboratory may then be made eligible for energy reduction. An example of this would be a space that relies on general ventilation and dilution of the room when using chemicals when the proper procedure is to use chemicals in a fume hood. Improving safety practices such as this may transition a space that was a poor candidate into being a good candidate for energy optimization.
In some situations, the assessment determines that the current ventilation in a space is adequate. In other cases, it has been revealed that the ventilation needs to be increased to improve safety based on the hazards present. This is another example of how the control banding process can improve safety in addition to identifying candidates eligible for energy reduction.
The Three Phases of a Laboratory Energy Reduction Program
There are three main phases of the laboratory energy reduction project. It begins with a study and analysis phase, the most important phase of the project.
Phase 1: Study and Analysis
Phase 1 is where the project team lays the foundation for the whole project. In this phase, stakeholders are identified and interviewed, site walkthroughs are performed, and existing equipment is inspected to observe existing conditions. These steps allow the project team to identify any required corrective measures to existing systems, determine which ECMs are viable, and develop execution plans for how to implement the potential ECMs. All findings and execution plans are then presented to the stakeholders and their feedback is gathered. Once all feedback is received and reviewed, the project’s scope of work and execution plans are finalized. It is critical to make sure every stakeholder understands what is happening in the project, how the work is being executed, and how it is going to affect them.
Phase 2: Implementation
Next is the implementation phase that starts with a meeting to re-introduce the project to all the stakeholders and make sure they are aware of and understand the work to be undertaken. This is followed by site walkthroughs with stakeholders to point out exactly what equipment will be affected and how, review execution plans and SOPs, and assess any planned changes to laboratory policies and procedures. Once the work is underway, it is important to evaluate the effectiveness of the execution plan and SOPs and make adjustments, as needed.
Throughout this entire phase, constant communication with all stakeholders must be maintained. Nearly every project will experience delays, so it is critical to constantly be updating the project schedule and notifying everyone involved. Most laboratory energy-reduction projects occur in live laboratory buildings with active research. Be aware that the project schedule may impact the occupants schedule who may have ongoing research that cannot be compromised by schedule changes. Another issue to be aware of is the possibility for maintenance to be required on building systems while the project is ongoing. For example, if a heating or cooling issue occurs in the same space being worked on by the project, it is important to know who will be responsible for addressing the issue.
Phase 3: Measurement and Verification
Lastly is the measurement and verification phase. In this phase, a commissioning process should be performed to verify that the work executed matches the work planned and that any deficiencies are identified, documented and corrected. This step is important for all projects but is doubly important for laboratory energy-reduction projects due to their impact on ventilation and safety. It is important to make sure the building systems (HVAC systems, control systems, and laboratory equipment, etc.) are operating correctly when the work is complete, and that the institution is knowledgeable and prepared to provide the required maintenance. This may include training of occupants and updated signage for laboratory spaces. It is important to work closely with EHS staff during this phase.
Once it is verified that the work has been implemented and is functioning properly, the effectiveness of the ECMs should be monitored over time. Thorough monitoring is suggested for at least one year after project completion to observe building performance throughout all seasons. This will increase the likelihood that any remaining issues are identified and corrected and that the achieved savings are maintained.
Without this ongoing monitoring, issues can occur that do not readily present themselves as problems but negate savings none the less. One example is a failed occupancy sensor that, through engineering controls, prohibits any ventilation setbacks. In this example, the ventilation and space temperatures would remain at acceptable levels for occupancy, but the system would not adjust the ventilation rates for unoccupied periods, effectively negating thousands of dollars in savings. Similar monitoring should be performed on laboratory equipment such as fume hoods to monitor face velocity and other metrics.
Laboratory energy-reduction programs succeed by effectively communicating the project plan and prioritizing occupant safety. In securing stakeholder buy-in, your program will get off on the right track to help achieve energy saving goals. Employing the control banding process will help ensure identification of laboratories that best qualify for ECMs without compromising safety or research.
Want to learn more about how to ensure your laboratories are properly qualified for energy reduction measures? Contact us today.
Subscribe
to our blog
"*" indicates required fields