Setting the Record Straight: Common Misconceptions about the Building Commissioning Process
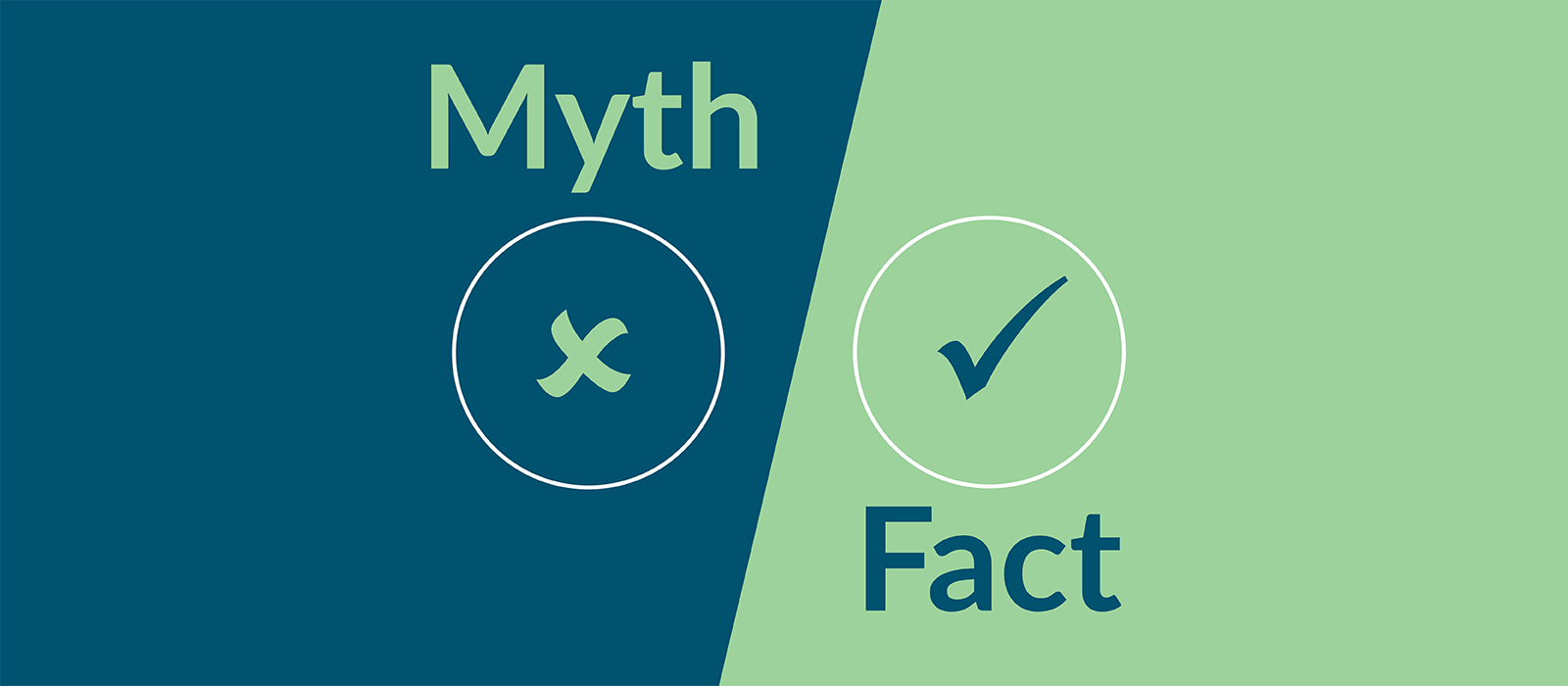
The building commissioning process offers owners a critical opportunity to confirm that their newly completed building meets design expectations and delivers as promised. Typically conducted by a third party, new building commissioning serves as a quality assurance measure, ensuring owners receive what they paid for. This step is crucial because, once the building is occupied, the owner inherits responsibility for any performance issues or problems that arise.
However, not all commissioning processes are equal. An incomplete or insufficient commissioning scope can leave you vulnerable to undetected issues, voided warranties, construction rework and costly repercussions. To help you avoid these risks, we are clearing up nine common misconceptions about the building commissioning process.
1. Energy Usage Is a Product of the Energy Model
This is one we encounter frequently and is a source of frustration for building owners and managers. In reality, actual energy usage is influenced by how equipment is installed and operated, not solely by the energy model. Without verifying that equipment installation meets contract requirements, the reliability of the energy model as a predictor of energy usage is uncertain.
Additionally, discrepancies between actual energy usage and the energy model can arise if the model was developed early in the design process and never updated to reflect the final design. A comprehensive building commissioning process includes confirming predicted energy usage through a calibrated energy model, ensuring alignment with real-world performance.
2. The Commissioning RFP Ensures a High-Performing, Reliable, and Safe Building on Day One
More frequently than you may think, we see Commissioning Requests for Proposals (RFPs) that have scope gaps. Too often, RFPs are written with a narrow focus on individual systems, such as testing the HVAC air distribution systems, without considering the critical interdependencies among the main and subsystems. Building systems do not work in isolation.
For example, an RFP that focuses on HVAC commissioning overlooks the critical interaction air distribution systems have with fire and other life-safety systems. In a real-world fire scenario, the HVAC system must respond appropriately to the fire alarm, shutting down to prevent fresh air into a fire. A key component of integrated systems testing is to make sure the fire alarm system functions correctly with the HVAC air distribution system. Without commissioning these systems in concert, you can’t be confident they’ll interact together and function correctly in an emergency. This siloed testing approach leaves significant gaps in the commissioning scope, potentially compromising the overall building performance and safety. True end-to-end commissioning requires a comprehensive approach to integrated system testing to ensure proper building performance and operation.
Scope gaps in RFPs often stem from knowledge gaps and miscommunication, among building owners, owner’s project managers, and other stakeholders, about the true scope of building commissioning. They may not fully understand the interconnected nature of building systems and the importance of integrated testing. Consequently, these gaps often become apparent later in the project, typically when the construction contingency is depleted. Addressing these oversights requires costly and disruptive change orders to bring in additional commissioning services, impacting both budget and schedule.
A comprehensive commissioning RFP, on the other hand, would outline the need for integrated systems testing across all disciplines—HVAC, plumbing, electrical, fire and life safety, and others—ensuring a fully functional and safe building.
3. Schedule Delays Can Be Resolved by Adding Construction Personnel
While it might seem logical to add more construction personnel to recover from schedule delays, this approach often falls short, especially for commissioning activities. Since commissioning focuses heavily on testing fully completed systems, adding more crew members during construction doesn’t necessarily speed up the process.
For example, fire alarm system testing involves verifying components such as fire alarm devices, electrical connections, control system integration, HVAC integration, elevator integration, and architectural elements. These tests cannot be performed if the fire alarm team is still completing their work. Similarly, infrastructure limitations may prevent additional personnel from expediting tasks effectively.
A better strategy is to proactively predict and address scheduling risks, such as prerequisites, delivery schedules, and project changes, rather than trying to compensate for delays as the occupancy date approaches. Commissioning deliverables like pre-functional checklists, equipment startups, controls point-to-point testing, air and water balancing, and issue resolution reports, are valuable tools for gauging project schedule status and ensuring progress aligns with completion goals.
4. An Occupied and Operational Building Has Achieved Its Full Value
Buildings often are occupied and operational before they are fully completed. While an occupancy permit verifies the life safety systems required for occupancy, many other critical systems may remain unfinished or only partially functional.
Even systems that are operational may not be performing to their full design intent. For example, a ventilation system may be designed to adjust the percentage of outside air based on building demand. However, if the system hasn’t been properly tested and balanced, it may fail to perform as intended.
Achieving the 100 percent performance verification target of commissioning requires that the building be fully complete, with all systems functioning as designed not merely occupied and operational.
5. Similar Equipment Will Have the Same Completion and Performance Status
Testing only a few pieces of the same type of equipment to represent all units in a building is a risky shortcut. For example, if a building has multiple air-handling units, the performance of each unit and the ventilation zone or system it integrates with must be individually tested. There are too many variables that can impact equipment performance, including manufacturing differences, shipping conditions, and installation variations. Assuming that one air handling unit’s performance is representative of all could lead to undetected issues, which may compromise your building’s overall performance and functionality.
It’s also important to note that sampling strategies impact the building commissioning process, including scope, budget, and value. While sampling can be a useful tool, it must be applied judiciously to ensure critical systems are thoroughly verified.
6. Manufacturer Warranties Are Guaranteed
While most equipment comes with a manufacturer’s warranty, these warranties are contingent on meeting specific requirements. To ensure your warranty isn’t voided, you must adhere to the manufacturer’s guidelines for shipping, storage, installation, startup, and more. These factors mean that simply installing a product doesn’t guarantee it will perform as designed.
Equipment performance depends on the entire installation process, and it must be tested and measured to confirm it aligns with the original design specifications. The commissioning process verifies and documents that equipment has been installed according to the manufacturer’s requirements, ensuring your warranty remains valid and that your equipment operates as intended.
7. Performance Persistence Is Ensured Upon Initial Commissioning Completion
Commissioning provides quality assurance, but it does not guarantee long-term performance of equipment and systems. Even if equipment is fully commissioned and has a 20-year expected lifespan, its actual performance depends on several variables beyond the commissioning process, such as proper maintenance, operator training, and changes in facility load or usage.
The purpose of commissioning is to verify that the equipment and systems meet the design intent at the time of completion, ensuring you receive that for which you paid. Sustaining performance overtime requires ongoing attention to these additional variables.
8. Any Level of Commissioning Will Ensure Performance
The level of assurance commissioning provides depends on the rigor of the building commissioning process. For instance, as highlighted in the air handler example in misconception #4, if your commissioning budget covers only one unit, the performance of other units in the system cannot be guaranteed.
9. Equipment Start-Up Alone Will Ensure Performance
Equipment start-up is an essential step but doesn’t guarantee system performance. Each piece of equipment is part of a larger integrated system that also requires verification.
Using the air handler example, the unit might function properly during start-up, but it also connects to ductwork and supplies air to a space with various distribution components. Testing the individual air handler alone won’t confirm the performance of the entire ventilation system. Comprehensive integrated system testing ensures that all components work together as designed, providing full performance assurance.
Minimize Risk and Protect your Investment with Building Commissioning
New building commissioning is a critical process designed to protect building owners by reducing future risks. Even in lower risk buildings, such as office spaces, significant financial consequences can arise from performance issues. By pursuing a comprehensive commissioning program for your new building, you can move forward with confidence, knowing every system and component is functioning as intended.
If you’re constructing a building or new space and want to ensure you’re getting the system performance you paid for, contact us today.
Subscribe
to our blog
"*" indicates required fields