New EPA Regulations Require Rigorous Safety Standards for Methylene Chloride Use in Laboratories and Industries
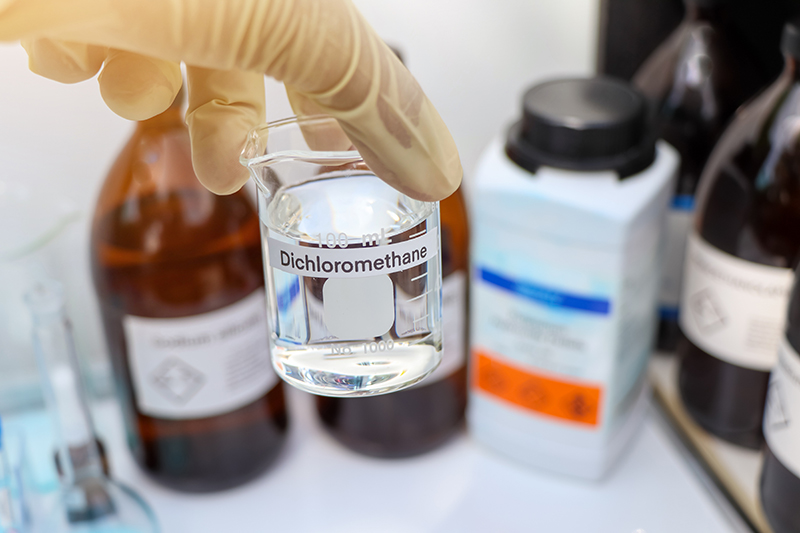
Notice: Compliance Update
In May 2025, the U.S. Environmental Protection Agency (EPA) proposed extending several compliance deadlines under its final risk management rule for methylene chloride. The proposal includes an 18-month extension for non-federal laboratories to meet Workplace Chemical Protection Program requirements, aligning their timeline with that of federal labs and contractors. The goal is to support long-term, sustainable compliance.
While the proposed changes are under review and public comment, current deadlines remain in effect until formally updated. That said, EPA has stated that enforcement of the existing deadlines is a low priority and intends to focus resources on the revised dates, once finalized. However, the agency still retains the authority to act in cases posing significant threats to human health or the environment.
Despite the potential delay, EH&E recommends that clients continue preparing for compliance now. This includes identifying methylene chloride tasks and initiating exposure monitoring. In our experience, the new exposure limits are difficult to meet in many lab environments and often require enhanced controls that take time and resources to implement.
Delaying compliance activities could leave organizations unprepared when the new deadlines become official and could result in rushed, less effective implementation. Early planning and action will better position laboratories to meet the regulation’s demands while minimizing workflow disruptions. Starting early will help minimize disruptions and ensure readiness.
Methylene chloride, also known as dichloromethane or DCM, is one of the most widely used laboratory solvents because of its relative versatility, low boiling point, and chemical stability. It’s also highly toxic due to the chemical’s potential to cause acute and chronic health effects, such as cancer, through inhalation or dermal exposure.
In 2019, the U.S. Environmental Protection Agency (EPA) first banned the commercial use of methylene chloride in paint and coating removers. In May 2024, the EPA issued a final rule under the Toxic Substances Control Act (TSCA) that expanded the prohibitions on most methylene chloride uses but allows for its controlled use in certain applications, including laboratories, when handled with rigorous worker protections, such as ventilation, PPE, and worker training. Consumer use will be phased out within a year, and most industrial and commercial uses will be prohibited within two years.
Under the new TSCA rule, the EPA allows the continued use of methylene chloride as a laboratory chemical, with stringent requirements to assess and control employee exposure to this chemical. Labs in biotechnology, higher education, hospitals, and pharmaceutical companies, which already may be subject to an Occupational Safety and Health Administration (OSHA) Standard for this chemical, are required to implement and manage the EPA’s regulatory requirements beginning in 2025.
Most impactful for laboratory workplaces, the EPA’s final rule mandates a Workplace Chemical Protection Program (WCPP) with stricter occupational exposure limits (OELs) and dermal protections than required for methylene chloride under OSHA.
Navigating OSHA vs. EPA Standards
Organizations with applicable labs have long been required to follow OSHA’s Occupational Exposure to Hazardous Chemicals in Laboratories standard (29 C.F.R. 1910.1450), which protects lab workers who handle hazardous chemicals and OSHA’s Methylene Chloride Standard (29 C.F.R. 1910.1052), which if warranted requires monitoring, control measures, recordkeeping, regulated areas, and medical surveillance. The EPA has designed their WCPP requirement, so it is similar to OSHA’s standard for methylene chloride, although there are some important differences.
OSHA’s Laboratory Safety Standard requires organizations with applicable labs to develop a Chemical Hygiene Plan (CHP) to address how to safely procure, store, handle, and dispose of chemicals. Employers with labs must also follow the OSHA Permissible Exposure Limits (PELs) for chemicals in workplace settings. For methylene chloride, OSHA’s PEL is 25 parts per million (ppm) as an 8-hour time-weighted average (TWA) and 125 ppm for a 15-minute short-term exposure limit (STEL).
In contrast, the EPA’s WCPP requires facilities owners and operators using methylene chloride to take appropriate measures to meet new inhalation exposure limits, which do not exceed 2 ppm as an 8-hour TWA and 16 ppm as a 15-minute STEL. The EPA requires initial exposure monitoring for any laboratory that uses methylene chloride (unless recent data from within five years can be used to demonstrate exposures are below the exposure limits under the new EPA rule). Note that because the new EPA limits are so far below the OSHA limits, it is possible that existing exposure monitoring data that organizations have are not low enough to demonstrate compliance with the new EPA standard.
Organizations with labs that use methylene chloride have a series of EPA compliance deadlines under the TSCA final rule for methylene chloride, beginning in 2025. These organizations are mandated to complete an initial monitoring assessment and if exposures exceed the new limits, demarcate “regulated areas” and provide respiratory protection within specified timeframes.
The deadline is May 5, 2025 for existing facilities and within 30 days of initiating use for new facilities. Organizations with labs must adhere to methylene chloride inhalations exposure limits and provide respiratory and/or dermal protection, if applicable, to existing facilities before August 2025 and within 90 days of initial exposure monitoring for new facilities.
A WCPP must be developed and implemented for existing facilities by October 2025. Periodic monitoring must be conducted, as a minimum, every five years. If possible, it is best to work with a chemistry department to eliminate the use of methylene chloride or replace it with a safer alternative.
The Impact on Labs
Individuals responsible for safety and compliance in their labs, such as environmental health and safety (EH&S) and Industrial Hygiene (IH) professionals, need to understand the EPA’s new rule on methylene chloride, the associated deadlines, as well as figure out how to navigate both OSHA’s regulations/standards and the EPA’s requirements, which can be confusing and time-consuming.
The EPA has stated organizations with labs can use existing chemical hygiene plans to fulfill some of the documentation requirements listed in the WCPP. For large organizations, such as major biotechnology, hospitals, pharmaceutical companies, and universities and colleges, the time and costs to comply with the EPA’s new regulations are more feasible compared to smaller organizations that don’t have the same resources.
How EH&E Can Help
As a trusted partner, EH&E offers comprehensive solutions to help organizations, especially smaller ones, navigate the complexities of EPA’s new methylene chloride regulations. Our experts provide tailored guidance, from initial assessments to ongoing compliance support, ensuring adherence to both EPA and OSHA standards. We specialize in laboratory safety, assisting with CHP updates, exposure monitoring plans, control measure evaluations, and employee training programs. With our team of certified professionals, we can help your organization achieve and maintain regulatory compliance while prioritizing the safety and well-being of your staff.
Our experienced Certified Industrial Hygienists, Certified Safety Professionals, and Certified Chemical Hygiene Officers can help laboratories understand the specific requirements under the EPA’s new TSCA rule and OSHA’s standards by identifying areas where labs may not meet regulatory requirements. Contact us today to speak with an expert.
Subscribe
to our blog
"*" indicates required fields