Beyond ASTM Phase 1: Do You Need the Protection of a More Robust Environmental Site Assessment?
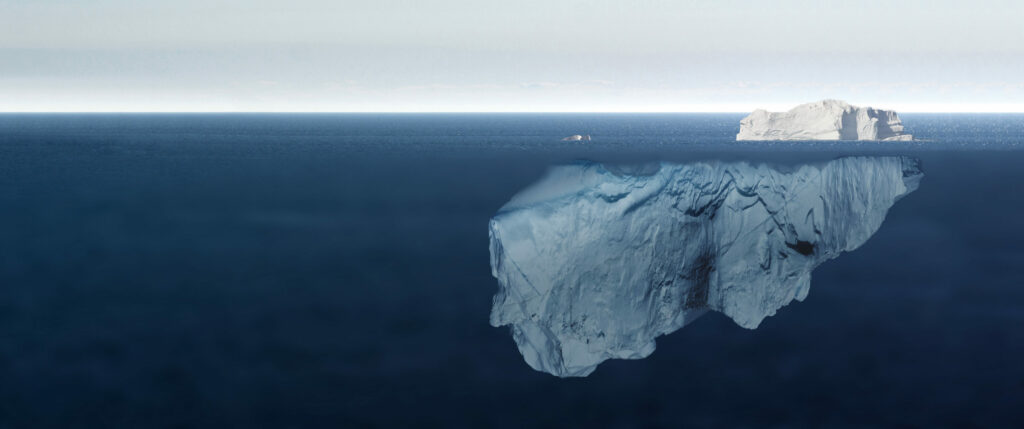
Purchasing or leasing a commercial property is a big decision, and you deserve to have a clear understanding of exactly what you’re buying. While your bank will require you to conduct an ASTM Phase 1 Environmental Site Assessment (ESA) to identify environmental issues associated with your new facility, this evaluation may not be comprehensive enough. Without a thorough environmental site assessment, potential costly liabilities and compliance issues could go unnoticed until it is too late.
So, how do you know when an ASTM Phase 1 ESA is enough? And how do you know when you need a more robust environmental site assessment? Let’s first discuss what a Phase 1 ESA covers, what it doesn’t and when you need to seek out a more extensive evaluation.
What is an ASTM Phase 1 ESA?
An ASTM Phase 1 ESA assessment follows a prescribed format to evaluate certain environmental conditions for a property. There are two primary components to a Phase 1 ESA:
- A visual reconnaissance of the property. No testing or measurement is conducted.
- A paper study to evaluate site use history and determine whether or not the property or nearby properties are included on environmental regulatory databases.
With just these two components, an ASTM Phase 1 has the potential to overlook substantial environmental and building condition issues. Unless there are obvious, visually recognizable or documented environmental conditions, the assessment won’t call for any further sampling or analysis. ASTM Phase I outlines protocols for assessment of other hazards such as asbestos, but these are not required. In fact, a Phase 2 assessment will only be triggered by finding something in the original ESA that is concerning to the buyer or lender.
To further cover their bases, new building owners and tenants often solicit an ASTM Property Condition Assessment, or PCA. While this assessment does take inventory of the building systems (e.g., HVAC, plumbing, elevators, building envelope, roofing, etc.), a standard PCA still doesn’t include testing or analysis of any kind. An ASTM PCA is an entry level assessment that utilizes a checklist approach but doesn’t “kick the tires”. Meaning building condition issues that could prove costly will be missed. For example, a standard PCA may not evaluate whether the existing HVAC system will need expensive upgrades to meet your intended use of the space. Something that could be critical if you intend to use the space for sensitive operations or a different use than the building was originally constructed for.
Plus, depending on the expertise of the person conducting your PCA, they may not have the complex understanding necessary to evaluate the full range of building systems. To fully evaluate a complex building, a comprehensive assessment should be completed by a team of specialists and often requires system testing.
When Further Assessments Are Needed
With a purchase or long-term lease for something as significant as a property, you don’t want to leave anything to chance. Failing to conduct thorough environmental and property condition assessments upfront can leave you with costly repairs, environmental response actions and code compliance issues, not to mention the potential delays to your construction and occupancy schedule. To further illustrate this importance, here are a few examples — drawn from real world scenarios — of when a Phase 1 ESA wasn’t enough.
- A new tenant was planning to renovate an old industrial factory. The Phase 1 ESA results largely focused on a written report of spilled hazardous materials that led to contaminated ground water. Unfortunately, what their Phase 1 assessment didn’t uncover was oil saturation in the floor slabs (an issue that can be hidden by some floor coverings or recent surface cleaning). The only way to fix the contamination was to completely replace the floor slabs or use costly chemical resistant sealants. EH&E has encountered this issue in multiple buildings with costs for clean-up ranging from many thousands to more than 1 million dollars. In some cases, this cost was absorbed by the tenant since it was not covered in the terms of their lease.
- A new owner purchased a building previously used for laboratory operations that involved hazardous materials. Concerned that the visual inspection of the ASTM Phase 1 wouldn’t be sufficient for discovering potential issues, this owner wisely brought in environmental and engineering experts to do a thorough assessment. Given the previous property use, EH&E conducted further testing and was able to uncover that the plumbing was contaminated due to substantial use of mercury — an issue that a visual inspection would not have identified. The fix would not be as simple as replacing the plumbing. It would require a complete upgrade to bring the systems up to current code, which would be very costly. Additionally, it presented a compliance issue because there would have been too much mercury going down the drains for reuse by the new occupant. Luckily, this owner was able to identify this environmental liability upfront before the purchase was complete.
- A biotech company moved into a new building that was previously used as a food production factory. This left behind unseen materials and residue on the floors that would allow bacteria to grow — inconsistent with the clean, biological-free workplace they would require for their sensitive operations. In addition to the risk of mold growth, a history of food processing operations can lead to odor issues for the next occupant. Since the previous use of the building didn’t involve hazardous materials, this issue would have gone completely unnoticed if the company didn’t seek out further assessment.
Beyond the costs associated with fixing these issues — whether for safety, aesthetics or to fulfill the new purpose of the building — there could be further complications depending on the specific scenario. For instance, consider the oil saturated floor slabs from the first example. Some oils, such as transformer oil historically used in electrical systems in mill and industrial buildings, contain polychlorinated biphenyls, or PCBs, which would then require disposal of flooring materials as hazardous waste. This is also a health issue with regulatory compliance requirements that can greatly affect the removal process and cost.
When You Need Further Expertise
It’s unfortunate, but true: it’s often difficult to know for sure that a Phase 1 ESA is sufficient. While certain factors put your property at greater risk for environmental liability, such as hazardous materials use history or age of the building, there are always unknowns. Plus, your planned use for the new property — and the regulations you’ll be required to meet — can have a big impact on the need for more evaluations.
Consider this: the basic Phase 1 ESA is generally conducted by someone who has extensive knowledge in environmental regulations related to soil and groundwater, but often do not have the expertise to connect the dots as to how potential liabilities would affect the whole building systems. Full due diligence requires the expertise of building scientists and engineers who understand the design and construction process and how building systems impact each other. While this may cost more upfront, savvy buyers know the potential financial savings and risk avoidance could be priceless, especially in the early stages of a new business venture.
If you have concerns about a property you are considering for purchase or lease, contact us today to discuss your environmental site assessment needs.
Subscribe
to our blog
"*" indicates required fields